连云港优质伺服压机设备
发布时间:2023-10-05 00:55:13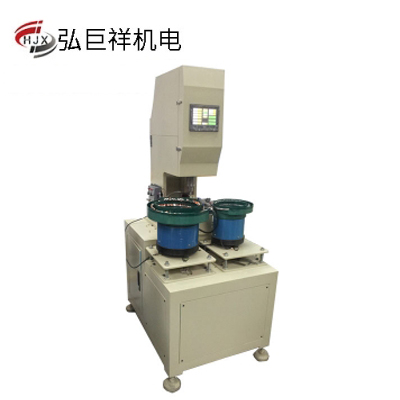
连云港优质伺服压机设备
在生产制做系统进程中以程序流程操纵,可以对不一样压装加工工艺开展频繁不一样的压装,是别的四柱液压机可高速冲床没法完成的工艺流程姿势系统进程,电子伺服压力机真正完成一机要用,降低产线支出和占地;电子伺服压力机可以同屏多种多样压装程序流程,历经不一样的实际操作按键或不一样的实际操作顺序完成频繁连续压装,压装机具备不错的方向操纵精准度,一台设备可以完成压装工艺流程的制做;电子伺服压力机的多加工工艺选择压装或顺序压装使生产线可以获得简单化,可以降低花费,可以有效操纵产品品质,可以节约人力资源成本。全部压装系统进程分成快放、勘查、压装、保压、回家五个环节。空行程安排的快放可以发展生产输出功率,压装系统进程的慢速度可以供求平衡稳定压装但是冲,保压可以防止压装机件的反跳,智能化判断可以快递分拣欠佳品,精准定位可以简单化工作服磨具,伺服电机操纵可以降低驱动力耗损,电动式传动系统可以降低噪声,改善工作自然环境。启动时设备会积极追寻标准端点,设定好主要参数后,按启动按键压头将再此方向以快放速率降低到勘查方向,随后以勘查速率降低,开始勘查系统进程。勘查系统进程直至所设置的勘查约束力方向中断,如来到勘查约束力方向还未勘查到钢件,压头将中断姿势,此时可按回零按键回家机械设备端点;如在勘查系统进程接触压力抵达预设值时,压头积极转换到压装速率开始压装钢件。压放到设置方向时将按客户所设置的保压時刻保压,保压時刻结束后压头以设置速率回家至所设定的作业面。
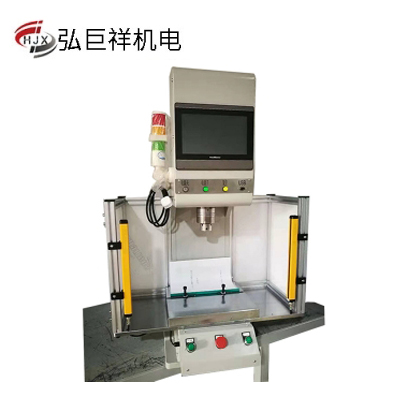
连云港优质伺服压机设备
1、的压装力、压入深度、压装速度、保压时间等全部可以在人机界面上进行数值输入,操作直观,简单方便。2、伺服压力机压装力与位移全过程曲线图可以显示在液晶显示触摸屏上,全过程控制可以在作业中的任意阶段自动判定产品是否合格,99.9%实时去除不良品,从而实现在线质量管理。3、可自行定制、存储、调用压装程序100套;七种压装模式可供选择,满足不同的工艺要求。4、通过外部端口连接计算机,可以将压装数据存贮在计算机中,保证产品加工数据的可追溯性,便于生产质量控制管理。5、由于机器本身就具有精确的压力和位移控制功能,所以不需要另外在工装上加限位,加工不同规格是只需调用不同压装程序,因此可以轻松的实现一机多用和柔性组线。

连云港优质伺服压机设备
选用液压缸时应注意密封件和工作油的影响密封件摩擦力大时,容易产生爬行和振动。为了减小滑动阻力,常采用摩擦力小的密封件,如滑动密封等。此外,密封件的耐高湿性、耐低温性、硬度、弹性等对液压缸的工作亦有很大影响。耐高温性差的密封件在高温下工作时,容易粘化胶着,密封件硬度降低后,挤入间隙的现象更加严重,进而加速其损坏,破坏了密封效果,耐低温性差的密封件在-10℃以下工作时,容易发生压缩永久变形,也影响密封效果;硬度低、弹性差的密封件容易挤入密封间隙而遭致破坏。聚氨脂密封件在水溶液中很容易分解,应该特别予以注意(详见第三章第十二节中有关密封件的选用)。工作油的选择,应从泵、阀、液压缸及整个液压系统考虑,还要分析液压装置的工作条件和工作温度,以选择适当的工作池。在温度商、压力大、速度低的俏况下工作时,一般应选用粘度较高的工作油。在温度低、压力小、速度高的情况下工作时,应选用粘度较低的工作油。在酷热和高温条件下应使用不燃油。但应注意,使用水系不燃油时,不能用聚氨醋橡胶密封件:用磷酸酣系不燃性油时,不能使用丁脯橡胶密封件,否则会引起水解和侵蚀。精密机械中应采用粘度指数较高的油液。除了机油、透平油、饺子泊外,还可以根据情况选用适当液压油,如精密机床液压泊、航空液压油、舵机液压泊、稠化液压油等。

连云港优质伺服压机设备
如何应对的失载?今天小编就来给大家介绍一下:一方面可认为液压机添加液体弹功能贮存量,一般来说,其液压缸中油液的高度和其间存储的弹性势能是成反比的,所以当机器俄然失载后,可以在机器的使命台和下模具的间隙间加一个垫板,使得横梁的作业行程上移,然后下降油缸缸中油液的高度。或者是在液压缸活塞和横梁间隙中加一个可动垫块,当机器向下运动时,活塞与横梁就能实现同步下落。可是加压后的话,活塞会由于垫块的效果而先回升,起到了添加液体弹性势能的贮存量的效果。正是由于油液的高度下降了,所以能量也不会俄然开释,失载的疑问也能减轻。为处理液压机俄然失载的疑问,还可以从其他门道开释能量,使得液压缸中高的低压液体可以迅速从周围卸掉。这种处理方法尽管效果显著,可是请求操作人员对机器的敏感度较高,避免对机器形成损坏。在液压机的下边增设一个缓冲垫,可对机器进行缓冲,下降机器轰动,而且有些能量还会耗费到缓冲垫上,有用削减对机器的损害。